In cold chain logistics, precision is everything. A few degrees of deviation — even for a few minutes — can compromise vaccines, spoil fresh produce, or render pharmaceuticals unusable. But why do temperature fluctuations happen even in highly controlled environments?
Understanding the science behind temperature instability in cold chains is the first step toward preventing product loss, maintaining compliance, and building trust with customers.
What Is a Cold Chain?
A cold chain is a temperature-controlled supply chain used to preserve and transport sensitive products. This includes:
-
Vaccines and pharmaceuticals
-
Dairy and meat products
-
Frozen and chilled food
-
Biotech and lab samples
Most cold chains require storage between:
-
2°C to 8°C for vaccines
-
-18°C or lower for frozen goods
-
0°C to 4°C for chilled items
Maintaining this range is critical — but far from easy.
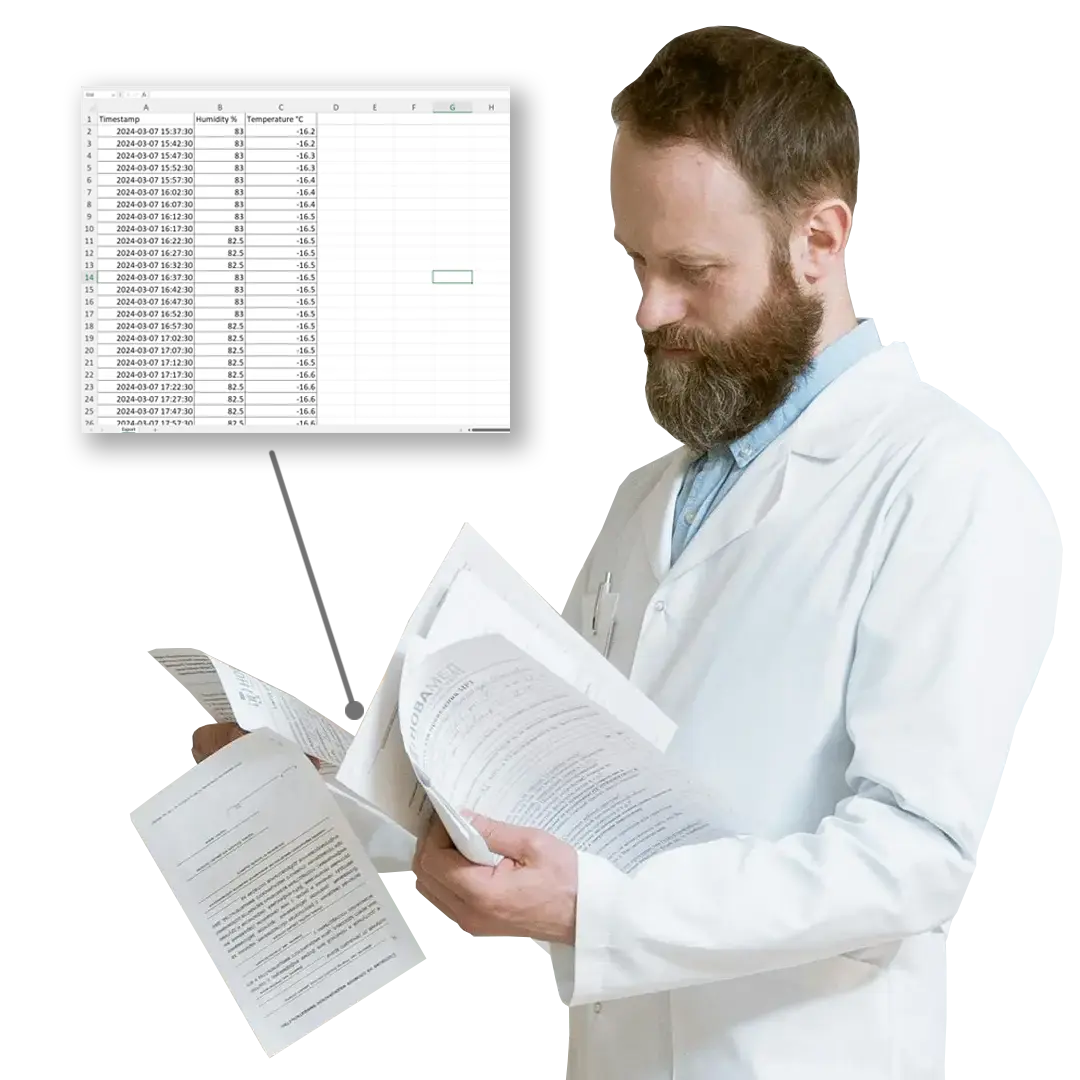
Why Do Temperature Fluctuations Happen?
Despite refrigeration systems, cold chains are vulnerable to scientific and environmental factors that cause instability.
1. Thermal Mass and Heat Transfer
When warm items are placed into a cooler environment (like a refrigerated truck), they:
-
Radiate heat to the surroundings
-
Temporarily raise the ambient temperature
-
Take time to reach equilibrium (known as thermal lag)
Scientific principle: Heat flows from warmer to cooler objects until thermal equilibrium is reached.
2. Door Openings and Air Exchange
Each time a cold room or transport vehicle is opened:
-
Warm, humid air enters
-
Cold air escapes
-
The internal temperature rises rapidly, especially near the door
Even a 30-second opening can lead to several degrees of fluctuation, depending on the insulation and outside environment.
3. Load Distribution and Air Circulation
Improper stacking of cartons or pallets blocks airflow, creating:
-
Hot spots far from cooling vents
-
Uneven cooling
-
Delayed temperature recovery after defrost cycles
Science tip: Cold air is denser and sinks, so proper vertical circulation is essential.
4. Compressor and Defrost Cycles
Refrigeration units run in cycles to conserve energy. During the defrost cycle:
-
The system temporarily warms internal coils to remove frost
-
Temperature briefly rises
-
Poorly insulated loads may be affected
Even though these are short and controlled, frequent cycles or poor system tuning can affect sensitive cargo.
5. External Temperature Extremes
Transporting cold chain goods through hot or humid regions increases stress on insulation and cooling units. Trucks or containers left under direct sunlight can experience:
-
External walls heating up
-
Conductive heat entering through walls, floor, or roof
-
Higher compressor load and risk of failure
The Scientific Terms You Should Know
Concept | What It Means |
---|---|
Thermal inertia | How slowly an object changes temperature |
Heat flux | The rate of heat transfer through a surface |
Latent heat | Heat absorbed or released during phase change (e.g. melting) |
Insulation value (R-value) | Measure of how well a material resists heat flow |
Why Temperature Excursions Are So Dangerous
Even short-term temperature deviations can lead to:
-
Vaccine spoilage and loss of efficacy
-
Bacterial growth in perishable foods
-
Non-compliance with WHO GDP, HACCP, and other standards
-
Reputational damage and loss of customer trust
Regulatory bodies like SFA, WHO, and FDA require continuous, verifiable records of cold chain conditions — and that includes explanation of any anomalies.
How IoT Monitoring Solves the Problem
Modern cold chain operators are now turning to IoT-based monitoring systems to:
-
Detect temperature fluctuations in real time
-
Send instant alerts to prevent product loss
-
Identify root causes through data analysis
-
Maintain digital records for audit trails
MWI’s system uses:
-
Wireless sensors for freezers, fridges, and trucks
-
Cloud dashboards to visualize trends and patterns
-
Configurable alerts based on your exact thresholds
-
Long-term logs to identify recurring fluctuation points
Proactive Science = Better Cold Chain Outcomes
By understanding the physics behind fluctuations, operators can:
✅ Optimize warehouse layout for airflow
✅ Minimize door opening times
✅ Use pre-cooling for new inventory
✅ Improve insulation or choose better containers
✅ Place sensors in high-risk zones (e.g., door area, top shelf)
Real-World Example: Pharma Distributor in Singapore
A pharmaceutical distributor using MWI’s IoT monitoring system discovered that daily 8AM restocking led to repeated spikes above 10°C in their cold room.
Root cause? Workers were leaving the door open for 3+ minutes.
Fix: They re-trained staff, adjusted scheduling, and added visual door-close timers. Fluctuations dropped by 95%.
Other Blogs
Food Storage
Medical Storage
IT Equipment
Server room temperature & humidity monitoring